INTRODUCTION
Porcelain fused to metal restorations are one of the increasingly popular restorations in recent years due to increased demand for esthetic appearance, durability and versatility of use for fixed partial dentures, metal ceramic restorations combine the natural esthetics of a brittle material such as porcelain with durability and marginal fit of a metal casting. Ceramo-metal restorations have been the most preferred choice in the treatment of restorable or missing teeth .The very mention of ceramo-metal restorations brings to mind, its composite material nature and the vital importance of the porcelain/metal interface. Evaluation of porcelain metal bond has been a subject of immense interest in the recent past and studies have proved that the optimal temperature and the atmosphere in which the porcelain is baked on to the metal surface is of critical value. For porcelain fused to metal restorations to be clinically successful, it must satisfy certain criteria. Apart from other criterias, adequate physical property to provide strength and rigidity and quality of porcelain-metal bond are two main criteria which are very essential for a restoration to be clinically successful. Vacuum firing of porcelain has yielded favorable results. This led to the thought that an inert atmosphere would produce better ceramo-metal bonding and because of this, firing of porcelain in an atmosphere of argon gas has evident great interest, it seems pertinent to evaluate the bond strength of porcelain to non precious metal copings under different firing atmospheres (vacuum and inert).
MATERIALS AND METHODS
The commercial ceramo-metal (base metal) alloy Naidur and Ceramco3 porcelain were selected in the study with composition of base metal is nickel-59-64%, chromium-22-27%, molybdenum- 10-12%, silicon-1.4-1.6%. Methodology consists of three steps
1) Preparation of cast base metal alloy.
2) Preparation of porcelain fused to metal sample.
3) Sample preparation for microstructural evaluation by scanning electron microscope
Preparation of cast base metal alloy
Eighteen cylindrical and eighteen rectangular shaped wax patterns were formed. The dimensions of rectangular shaped wax patterns were 10mm X 10mm X 5mm and cylindrical shaped wax patterns were 2.5mm in diameter and 60mm in length. Wax patterns were invested in phosphate bonded investment material. Burnout of wax and casting of base metal alloy into the mold was done. Finishing was completed with carbide trimmers.
Preparation of porcelain fused to metal sample
Ultrasonic cleaning of the cast base metal alloy samples was performed. Application and firing of opaque porcelain layer on the cast base metal alloy samples was done under different firing temperatures, that is 960oC, 9750C,9900C, at different firing atmospheres (vacuum and argon).The groups were named as A,B,C,D,E,F and G. The firing atmosphere of group A, B, C was vacuum and group D,E,F was argon. Each group consisted of six samples each in which 50% samples were of cylindrical shape and were denoted by A1-A3,B1-B3,C1-C3,D1-D3,E1-E3 and F1-F3 for bond strength testing and 50% samples were of rectangular shape which were denoted by a1-a3,b1-b3,c1-c3,d1-d3,e1-e3 and f1-f3 for scanning electron microscopic study respectively. Application and firing of dentin porcelain layer on all samples at recommended temperature is 930oC in their respective atmospheres.
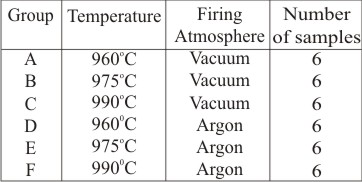 |
 |
Sample preparation for microstructural evaluation by SEM.
Transverse cross sections of the rectangular samples were cut and samples were mounted in cold setting compound liquid and powder. They were finished and polished with emery paper, alumina and diamond suspension. Samples were demounted and ultrasonically cleaned. Scanning electron microscopic analysis was done.
RESULTS AND OBSERVATIONS
Microstructural Evaluation
Group A to F – All samples in each group of rectangular shape.
Bond Strength Evaluation
Group A to F – All samples in each group of cylindrical shape.
Mean Shear Bond Strength with Standard Deviation and Standard Error of Group A-F samples
Shear bond strength was maximum in Group E (opaque porcelain layer fired under argon atmosphere at 975°C) than in Group B (opaque porcelain layer fired under vacuum at 975°C)
SEM OBSERVATIONS
Scanning electron microscopy was done on all the samples to see the number, size, shape and distribution of pores. At lower magnification, comparison of interaction zone of porcelain fused to metal samples at different firing temperatures and different firing atmosphere using Scanning Electron Microscope (SEM) shows that pores were found aligned along the interface on the porcelain side in all the samples. However, the number, size, shape and distribution of pores was different in all the samples, depending on the firing temperature and firing atmosphere
DISCUSSION
The commercial ceramometal (base metal) alloy Niadur and Ceramco 3 porcelain were selected for the study. Niadur was easily available and most commonly used commercial base metal alloy. The Ceramco3 porcelain was selected as it was easier to manipulate and also easily available.
Shear bond strength was maximum in Group E (opaque porcelain layer fired under argon atmosphere at 975°C) than in Group B (opaque porcelain layer fired under vacuum at 975°C).It can be assumed that excessive oxide layer produced on firing was considered to have a potentially adverse effect on ceramo-metal bonding. It was found that firing in an inert atmosphere such as argon limited the excessive oxidation in some of the groups, which significantly increases the bonding strength of conventional Ni-Cr porcelain system.
It is evident from SEM investigation of Group A-F samples that the pores were commonly present in the porcelain side at the interaction zone. However, the number, size, shape and distribution of pores varied in all samples depending on different firing temperatures and atmospheres of opaque porcelain layer. It was clearly noted that as the firing temperature was increased, the pores became less in number as well as size of pores decreased. The least number of pores with least diameter were found at 975°C under argon atmosphere. It shows that porcelain particles flowed and filled up the air spaces between them optimally at this temperature resulting in better sintering, leading to very few numbers of pores. Another reason of less number of pores at 975°C under argon atmosphere might be the optimal match of coefficient of thermal expansion of porcelain and metal.
Also noted was the fact that the pores were present only in the porcelain side and not in metal side. This could be due to the reason that porcelain was a brittle material as compared to metal. Therefore, tendency of pore formation was greater in porcelain side.A relatively thick layer of oxides was the cause of decrease in bond strength for the Ni-Cr porcelain system. The use of vacuum or an argon atmosphere when firing porcelain to Ni-Cr is. essential for control of non adherent oxide formation, to achieve a high bond strength.
A specially designed argon atmosphere porcelain furnace was used in this study (Lectra, Ugin, France). This furnace was designed to minimize the oxide formation between metal and porcelain by flushing argon into the firing chamber. The purity of the argon used in this furnace was 99.99% and the chamber was made of special heat resistant glass to minimize the residual oxygen present.The opaque porcelain layer applied to group A to F samples was fired at two firing atmosphere i.e. vacuum and argon. Argon atmosphere was selected because it was thought that inert atmosphere produced better porcelain metal bonding. In each firing atmosphere, PFM samples were fired at three different firing temperatures i.e. 960°C, 975°C and 990°C.
This range was selected due to some reasons.It was found that opaque porcelain layer was most oftenly fired in the temperature range of 960°C to 975°C.Therefore, firing temperature of 960°C and 975°C were selected. 990°C temperature was selected to evaluate the changes below the most commonly used temperature range and above the manufacturers recommended temperature respectively. Shear bond strength of all samples were tested in a universal testing machine.
So overall analysis shows that shear bond strength was maximum in Group E (opaque porcelain layer fired under argon atmosphere at 9750C).It can be assumed that excessive oxide layer produced on firing was considered to have a potentially adverse effect on ceramo-metal bonding. It was found that firing in an inert atmosphere such as argon limited the excessive oxidation in some of the groups, which significantly increases the bonding strength of conventional Ni-Cr porcelain system.
CONCLUSION
Within the limits of this study, the following conclusion were drawn.
1. Differential statistical tests suggested that higher bond strength were obtained, when PFM samples were fired in argon atmosphere as compared to vacuum.
2. Among argon fired samples, bond strength was highest in group E samples (opaque porcelain layer fired at 9750 C) and least in group F samples (opaque porcelain layer fired at 9900 C).
3. Among vacuum fired samples, bond strength was highest in group B samples (opaque porcelain layer fired at 9750 C) and least in group C samples (opaque porcelain layer fired at 9900 C).
4. It can be concluded that highest bond strength, among all the groups was in group E samples ( opaque porcelain layer fired at 9750 C under argon atmosphere) followed by group B samples samples (opaque porcelain layer fired at 9750 C under vacuum).
5. SEM photomicrograph of the tested base metal porcelain samples demonstrated that the interface of the argon fired sample conventionally i.e. in vacuum.
6. SEM analysis also indicated that least number of pores and least pores diameter was found in group E samples followed by group B samples. This could also support that bond strength was higher in group E samples compared to group B samples.
7. It can also be concluded that an optimum firing temperature of 9750 C under argon atmosphere is preferred for better adhesion properties of porcelain to Ni-Cr base metal alloy.
REFERENCES
1. Shell, J.S., and Nielsen, J.P.: Study of the Bond between Gold Alloys and Porcelain. J. D. Res., 41(6): 1424-1437, 1962.
2. O'Brien, W.J., Kring, J.E. and Ryge, G.: Heat Treatment of Alloys to be used for the Fused Porcelain Technique. J. Pros. Dent., 14(5): 955-960, 1964.
3. King, B.W., Tripp, H.P., Duckworth, W.H., and Battelle: Nature of Adherence of Porcelain Enamels to Metals. J. Am. Ceramic Soc., 42: 504, 1959.
4. Leone, E.F., and Fairhurst, C.W.: Bond Strength and Mechanical Properties of Dental Porcelain Enamels. J. Pros. Dent., 18(2): 155-159, 1967.
5. Pask, J.A., and Fulrath, R.M.: Fundamentals of Glass-to-Metal Bonding: VIII. Nature of Wetting and Adherence. J. Am. Ceram. Soc., 45: 572-575, 1962.
6. O'Connor, R.P., Mackert, J.R., Myers, M.L., and Parry, E.E.: Castability, Opaque Masking, and Porcelain Bonding of 17 Porcelain-Fused-to-Metal Alloys. The Journal of Prosthetic Dentistry, 75(4): 367-374, 1996.
7. Poggioli, J., Montagnon, J., and Lambart, J.: Rev. Franc. Odonot-Stomat., 15: 1215, 1968.
8. Sced, I.R., and McLean, J.W.: The Strength of Metal/Ceramic Bonds with Base Metals containing Chromium : A preliminary report. Brit. Dent. J., 132: 232-234, 1972.
9. Wagner, W.A., Asgar, K., Bigelow, W.C. and Flinn, R.A.: Effect of Interfacial Variables on Metal-Porcelain Bonding. J. Dent. Res., 62: 1229-35, 1983. |